
“Make it work, make it happen, and make it right. Once you create something, your name is on it"
Grocery Grabber
A COVID-19 Relief Project
Problem:
Grocery shopping is a necessary chore for many people across various communities. However, it is also a common place where people can be easily infected as various people have to touch items (products, carts, etc) that have been touched by others, and are sometimes in close proximity with other people.
As such, a solution must be implemented to help slow the spread of COVID-19 and make grocery shopping a safer process.


According to many scientists and reports, the grocery store should not be disregarded as a potential 'hotspot' for the coronavirus. Within weeks, "dozens of grocery store workers have died from coronavirus..." says CNN.
​
Biggest threats to grocery stores during pandemic:
-
Careless customers that infect other customers and front-line staff/workers
-
Limit to curbside pickups and home deliveries due to lack of hourly workers
-
In the US, the economic conditions made unemployment benefits earnings higher than regular hourly wages, causing people to stay unemployed for the time being​
-
-
Gloves have proven to be equally as dangerous to use if not removed and disposed of properly.
A simple, ideal solution...
After drawing inspiration by looking a simple garbage grabber, I understood that the simplest way to mitigate many of the problems listed above while ensuring a safe grocery shopping process after stay-at-home orders end worldwide.
-
Initially, attempted to use a regular grabber for grocery shopping:
-
The 'claw' part of the grabber was too big and long for grocery shopping
-
Also, due to the long arm of the grabber, it would make it harder to lift because of the additional torque applied.
-
-
Instead, in an attempt to give more control to the user and define functionality to be more aligned for grocery shopping, I came up with multiple designs that met the following conditions:
-
3D Printable
-
Easy to assemble
-
Takes a short amount time to manufacture
-
Easy to use during grocery shopping
-
Easy to carry and handle
-
The Design:
After brainstorming and thorough comparison of each design idea, I decided to try to implement a design that mimics that of tongs and scissors combined. This allows for the user to control the picking up of grocery items on their own terms.
​
To explain some basic design choices:
-
the 'gap' at the end of the grabber is to help hold handles, circular object, and fruits/vegetables.
-
The grabber only consists of two components making it easy and simple to manufacture.
-
I replicated the hand/finger holes based on an existing pair of scissors.
-
In the middle, one of the components has a pin, while the other component has a hole. The tolerancing of this joint is a tight fit. This allows the grocery grabber to be easily assembled and prevents from the two components from being easily disconnected.
​
The following 3D CAD Model was created on SolidWorks:
After brainstorming and thorough comparison of each design idea, I decided to try to implement a design that mimics that of tongs and scissors combined. This allows for the user to control the picking up of grocery items on their own terms.
​
To explain some basic design choices:
-
the 'gap' at the end of the grabber is to help hold handles, circular object, and fruits/vegetables.
-
The grabber only consists of two components making it easy and simple to manufacture.
-
I replicated the hand/finger holes based on an existing pair of scissors.
-
In the middle, one of the components has a pin, while the other component has a hole. The tolerancing of this joint is a tight fit. This allows the grocery grabber to be easily assembled and prevents from the two components from being easily disconnected.
​
The following 3D CAD Model was created on SolidWorks:
After brainstorming and thorough comparison of each design idea, I decided to try to implement a design that mimics that of tongs and scissors combined. This allows for the user to control the picking up of grocery items on their own terms.
​
To explain some basic design choices:
-
the 'gap' at the end of the grabber is to help hold handles, circular object, and fruits/vegetables.
-
The grabber only consists of two components making it easy and simple to manufacture.
-
I replicated the hand/finger holes based on an existing pair of scissors.
-
In the middle, one of the components has a pin, while the other component has a hole. The tolerancing of this joint is a tight fit. This allows the grocery grabber to be easily assembled and prevents from the two components from being easily disconnected.
​
The following 3D CAD Model was created on SolidWorks:
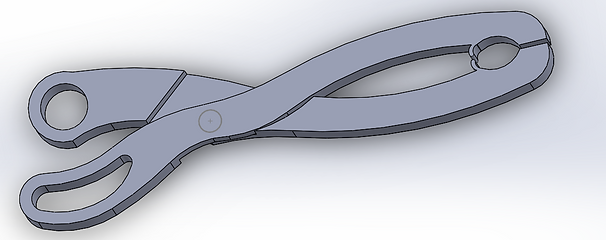
Material Selection:
In order to create a cheap and easy manufacturing process, but still maintaining the strength of the product. As such, there is only a handful of materials that can be selected such Sheet Metal, Plastic, and Wood/Timber. Out of these options, I determined that using plastic (specifically ABS or PLA) because:
-
Easy to implement / manufacture: allows for 3D Printing (anyone can print from anywhere)
-
Will be significant cheaper to use
-
Will be sufficient for grocery shopping.
-
The only drawback is the lack of recyclability of the material. If this product is no longer used, it will be hard to recycle it but it can be re-used for other purposes.

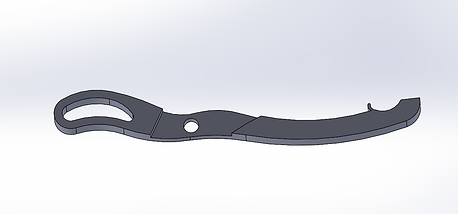
Simulation:
Before we begin to prototype and finalize the material selection, it is important to run some basic Finite Element Analysis (FEA) simulation to ensure that the current design can handle the loads and corresponding stresses. Through this analysis, one can identify any major changes that may be needed to implemented on designs and understand flaws in their designs before manufacturing it.
​
The first simulation I decided to run was to mimic the grocery grabber holding up a milk carton (one of the heaviest grocery items) to see if it could withstand the proper load and see which region of the grabber holds the most stress. Below is the forces applied to the FEA simulation:
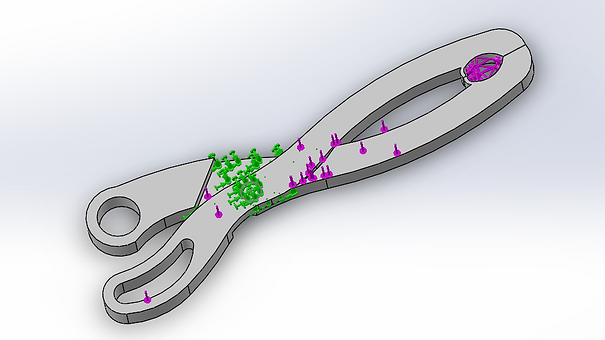
As seen in the image above, I have placed several forces as indicated in pink. Each set of arrows represents this:
-
Weight and Axial Pressure being applied on the gap end of the grabber
-
Gravitation force against near the center
-
Slight downward force from the hand near the finger holes
​
The green simply represents a fixture in the stress analysis. I applied a fixture in that region because that is the one point that remains relatively fixed when holding up a load.
​
The results from the FEA are below:

This screenshot depicts the stress distribution throughout the grabber mechanism. It shows how majority of of the grabber remains stress-free but the pin joint takes on some stress. However, the stress is not too great that such that the grabber will break. This ensures that the grabber will be able to support heavy grocery items in safe manner.

This screenshot depicts the displacement of parts of the grabber. As one can observe, the ends of the grabber experience greater deformation. However the maximum deformation that occurs under this high load is about 1.1 mm which is relatively small. This means that the grabber might slightly deform but it will not affect the functionality or quality of the product.

This screenshot depicts the strain on the product. Another great way to analyze the deformation on the product.
The second simulation I decided to run was to analyze the torsion acting on the pin joint as the grabber rotates (opening/closing). This was to simply ensure that the pin mechanism would not break easily which would make the product useless. Here are the FEA results:

This screenshot depicts stress on the pin of the grabber while torsion is acting on one end of the pin. Since the torsional force is provided by the other component as it rotates about the pin, the magnitude of torsion used for this simulation was not set at a very high value. The stress is higher near the bottom end of the pin but it's magnitude is insignificant. Thus, this confirms that the pin will not break when the grabber simple opens and closes.

This screenshot depicts overall displacement of the pin of the grabber while torsion is acting on one end of the pin. The simulation shows that there may be some negligent displacement near the top of the pin as the grabber rotates. This means the mechanism should work just fine and will not affect the functionality or quality of the product.
Prototyping:
Once I had finalized the CAD Model design on SolidWorks, I decided that the best way to prototype and physically test this product was through additive manufacturing, specifically 3D Printing. For the 3D Printing type, I decided to use the most popular and common one: Fused Deposition Modeling (FDM). The material was PLA. Since I did not have a 3D Printer and due to the restrictions placed by stay-at-home orders, it became hard to find options to prototype this grabber. Nevertheless, I managed to contact a local vendor who was kind enough to was able to quickly print the model for me. Below is a great first prototype:


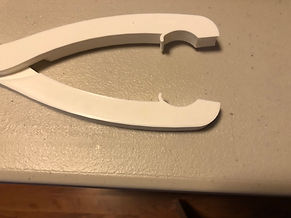
For the most part, the prototype ended up exactly like the CAD Design but there were a few manufacturing and design flaws that we spotted on the first review. First of all, the grabber is slightly misaligned in the sense that one half of the grabber is slightly higher than the other. This is a clearly a minor manufacturing issues that occurred during the 3D Printing process of this model.
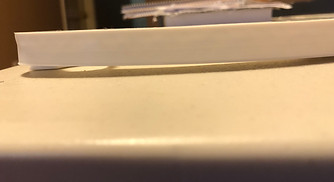

Upon holding the grabber and opening and closing it a few times, the grabber worked perfectly however I noticed that the 4-finger hole was slightly too small and it's edges were slightly rough, making it harder to hold comfortably. These count as minor design flaws. Other than that, the rest of the grabber seemed to be designed and manufactured as intended.
Testing:
Now comes the fun yet dreadful part of the project!
​
It's time to put the product's true functionality to the test and see if the Grocery Grabber can live up to its name. These are the main criteria that the grabber must be able to meet:
-
Can grab and hold small object that about the size of a pencil sharpener or school tape holder
-
Can grab and hold large, heavy objects such as milk cartons and large frozen food boxes
-
Can grab and hold circular objects such as jars, fruits, cans, etc.
-
Can grab and hold rectangular objects such as cereal boxes, packets, etc.
-
Can grab and hold items with handles like cups, milk cartons, etc.
​
So, I decided to the grabber with the following:
-
Flashlight for small objects
-
Nutella Jar for circular objects
-
Bread for rectangular objects
-
Milk Carton for heavy objects + handle

Holding the base of the flashlight with grabber. Diameter of base is as big as small objects.

Holding the nutella jar to test circular objects

The grabber is able to hold up the milk carton, however it requires two hands

Holding the base of the flashlight with grabber. Diameter of base is as big as small objects.
After testing the product, I was pleased to see that the grabber working for various objects. My family and I was able to easily pick up objects and place them elsewhere without requiring too much effort. However, the one limitation to the grabber was that it became hard to hold heavy object with just one hand. As seen in one of the images above, I had to hold the grabber with two hands to hold up a filled milk carton. But the grabber itself did not break. As such, after a running a few more tests with other heavy objects such as large water bottles and textbooks, I came to the conclusion that the grabber itself could only be changed slightly but the user still needs to put in effort from their end to lift the heavy object.
Product Lifecycle Assessment:
Ideally, my product is a Cradle-to-cradle product as it is 100% reusable after it has served its initial purpose. Therefore, we will perform the analysis in the circular economy perspective:
​
Raw Material Collection
-
Raw Material for PLA comes from corn starch or sugarcane, which are natural resoures
-
Materials are grown as crops and eventually, harvested
-
This process is mostly eco-friendly and relatively does not require the farmer to live in dangerous circumstances
-
However, agricultural harvesting requires use of automotive vehicles, herbicides/pesticides, etc.
-
Thus, there is the usage of gasoline/petroleum, electricity, and chemicals during this stage
-
Corn absorbs CO2 and produces glucose, which is a surplus to this product life cycle
-
Another con is that since large amount of corn are required to produce PLA, it may impact the food supply of such staple crops in society
​
Material Processing
-
Once collected, the corn goes through a wet milling process, where the starch is separated
-
To begin creating the PLA, starch is mixed with acid or enzymes and then heated
-
Later, it goes through a fermentation process and eventually forms into PLA Resin
-
Process requires use of chemicals and heavy machinery
-
Machinery means large use of electricity and fuel
-
Additionally, there are labor and maintenance costs, which also bring about slight health & safety concerns
-
Overall, this stage of the process needs to be handled carefully as it involves health & safety concerns and has some environmental & societal impact
​
Product Manufacturing
-
The product is 3D Printed
-
Process is to melt plastic at a high heat
-
PLA can release micro fine particles during printing which are slightly harmful
-
Some electricity is required to run the 3D Printer
-
Overall, very small energy usage and health risk associated with this stage
Transportation & Retail
-
Case 1: If 3D printed at home, then there is no transportation and retail needed. 0 energy usage and no health/safety factors.
-
Case 2: If the product is being printed at a 3D Printing facility and then being mass distributed, it will require vehicles like a van or large car to transport the product. This step requires the usage of gasoline or petroleum. Beyond that, it will also require the need of labor and their energy to help print and deliver these products. So, the step of the process requires some energy usage but there are little to none health/social issues.
Product Usage
-
There are no health risks associated when using the product and to the environment.
-
Since it is a purely mechanical product, it does not require any form of electricity and fuel. Just some basic energy input from the user.
End-of-life & Waste Disposal
-
When the product is no longer needed for grocery shopping, it can be easily used for various other kinds of grabbing and holding items for sanitary purposes. As such, the product is 100% reusable if the user chooses to do so.
-
If the user decides to dispose of the product, then there are some environmental impacts involved. Since the product is made of PLA plastic, it is biodegradable and can easily melt. This makes the product relatively eco-friendly. However, it takes time to degrade properly and as such, can cause some environmental harm.
-
To recycle properly, PLA plastic is required to be separated which requires the use of labor or machinery.
-
Once it has degraded, it just returns back to the environment and so the original materials (corn starch) is not completely wasted. Instead, it will continue the cycle as it will let more corn crops grow.
​
Sources:
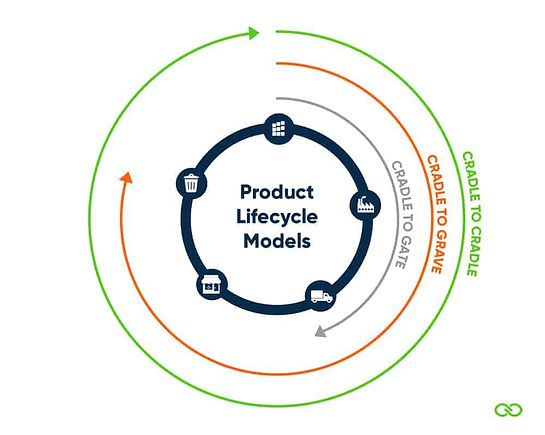
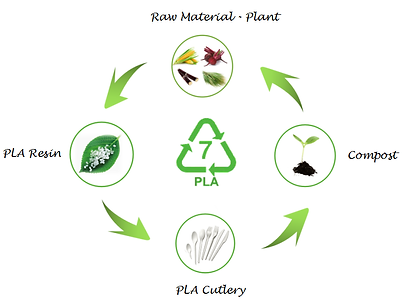
PLA life cycle. Credits: cngreenplastic.com.
Product Lifecycle Models. Credits: ecochain.com