
“Make it work, make it happen, and make it right. Once you create something, your name is on it"
Improved Bluetooth Speaker
Initial Product
The product is a portable Bluetooth speaker used seldom by my roommate. However, he planned on discarding the product as the clip part of the product broke easily (as seen in the photos). Instead, I decided to disassemble it and see what aspects of this product I could improve upon such that the product can be better in terms of functionality, cost, and sustainability.
During the disassembly of the product, I began to notice the difficulty and unnecessary effort it took to disassemble this product. This indicated plenty of issues with the assembly/manufacturing of the product and its poor 'recyclability' potential. For instance, in order to split the product in half, I had to take a knife and cut through the parting line of the product. After that, I had to take 3-4 screwdrivers (acting as levers) to forcefully remove the top half of the product.
In terms of functionality, the audio function of the speaker was working just fine, however the clip had a slight design issue. Specifically, the main clip arm interfered with the main body of the product after a particular angle (relative to the vertical axis). So, if the user were to continually force the clip past that small angle in an attempt to clip to something bigger, the clip and its pin itself will break off the product.
The following images show the different parts of the product during the disassembly stage:

Fully Assembled Product
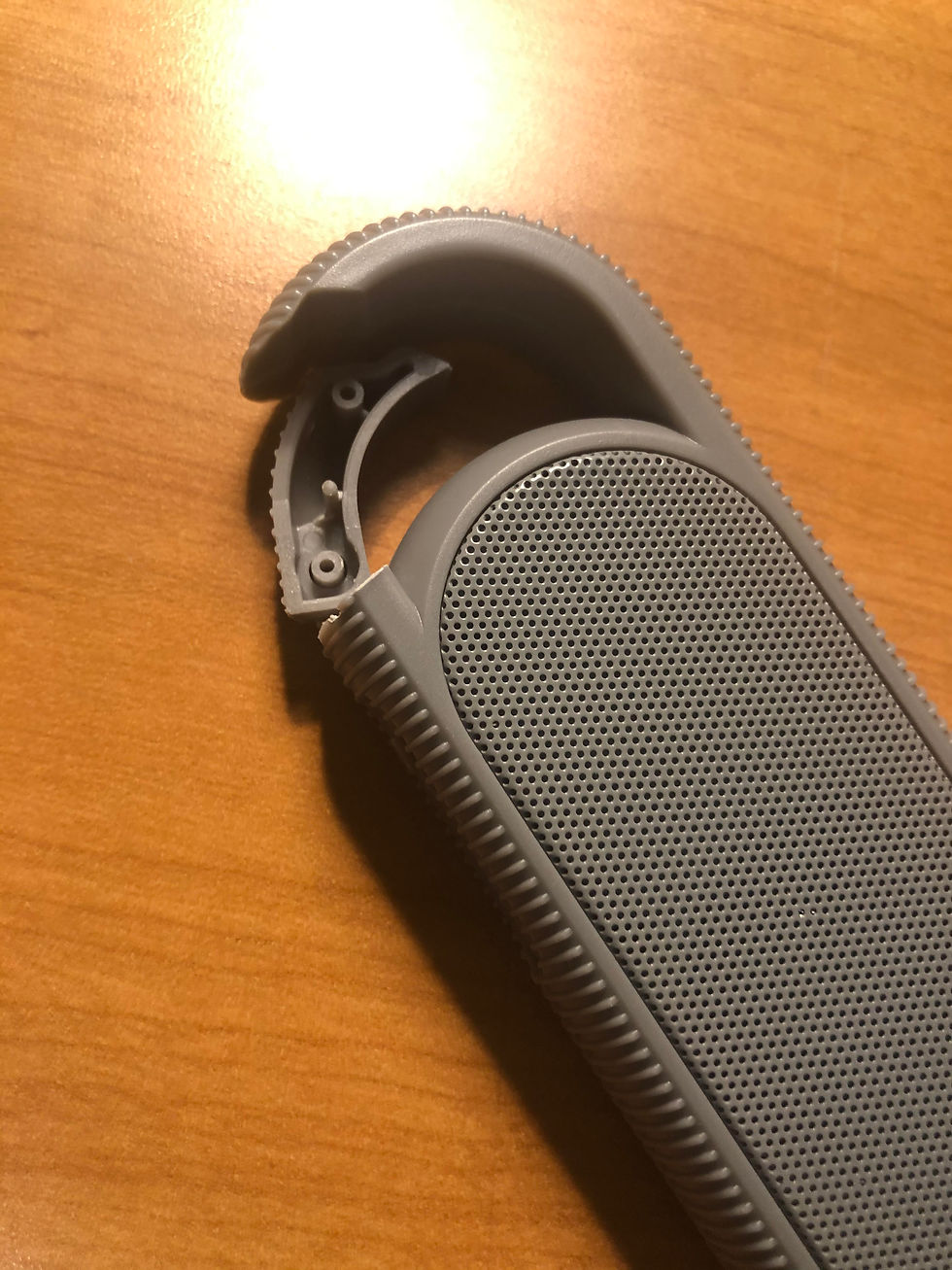
Clip System


Fully Assembled Product

Clip Halves
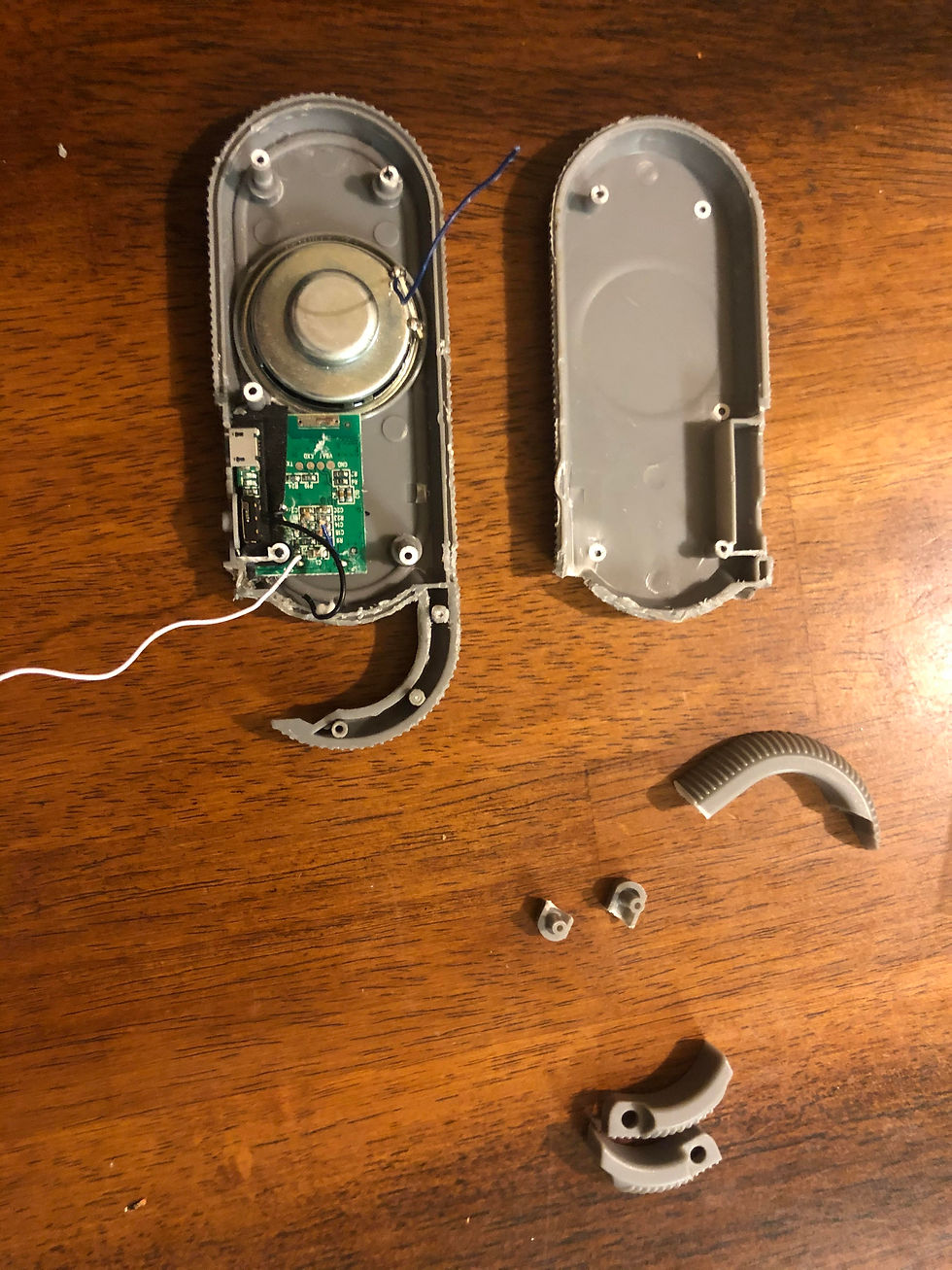
Product was split into two parts, internal electronics and components revealed
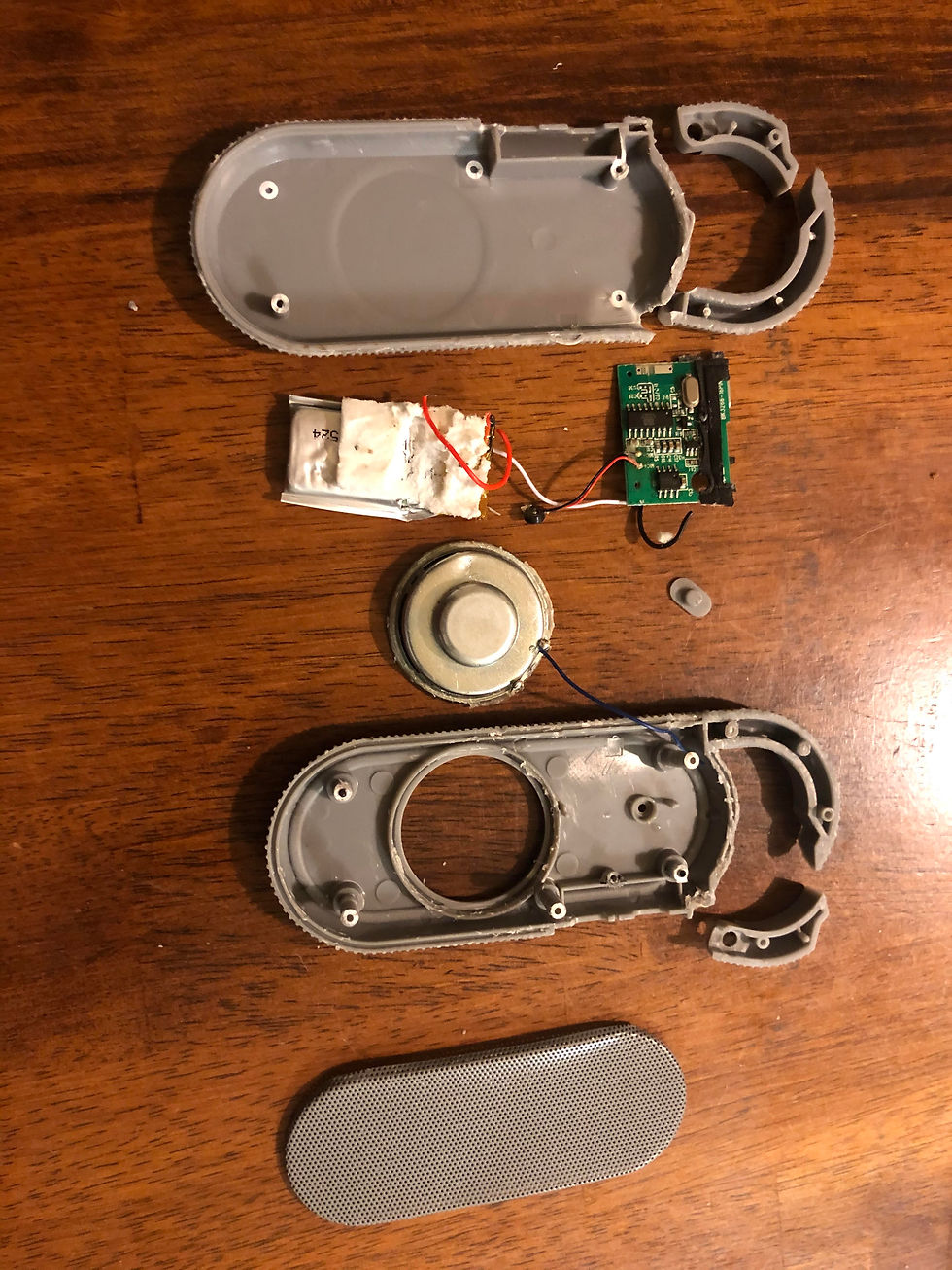
Fully Disassembled Product

Clip Halves
Bill of Materials
For a quick preliminary manufacturing analysis, it is important to develop a bill of materials to better understand the various components that make up this unique product.

Design for Manufacturing and Assembly (DFMA) Analysis
For a proper Design for Assembly (DFA) analysis, we must answer the following 4 questions and based on the answers, we can determine whether or not there is an “Opportunity to Combine or Eliminate?” parts in the existing product. From this, we can also determine the theoretical minimum number of parts. Besides that, we must also calculate the DFA index to completely evaluate the assembly process of the product.
4 Main Questions:
-
Can the part potentially be combined with any of the previously assembled parts because it can be made from the same material?
-
Can the part potentially be combined with any of the previously assembled parts because it does not move with respect to any other part?
-
Can the part potentially be combined with any of the previously assembled parts because it is not required to be separate to allow assembly of an internal part or parts (i.e. a cover plate or end cap)?
-
Can the part potentially be combined with any of the previously assembly parts because there is an alternative fabrication process that could be feasibly or economically adopted (e.g. typically a net shape process such as molding, casting, sheet metal stamping, etc)?
The following DFA table can help us reduce the number of components within the product by allowing us to see which products can be combined or eliminated based on the answers to the aforementioned questions. The second DFA table helps us better understand the assembly efficiency of the product as indicated by the DFA index. In this case, the DFA index (≅ 0.66) for the product is pretty good, but like Elon Musk once said, "There's room for improvement".


Computer Aided Design (CAD) 3D Modeling
I re-modeled the entire Bluetooth speaker on PTC Creo. The only parts that could not be remodeled were the mini loudspeaker and the lithium-polymer battery because they are purchased components and are not essential for the evaluation of the speaker.
Cover Top Half
Cover Bottom Half


Clip Bottom Half (Top View)

Clip Top Half (Bottom Half)

Clip Top Half

Button Slider

Electronic Circuit Board (PCB)
Speaker Mesh Grill

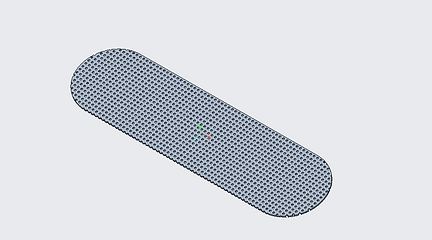
Final Assembly
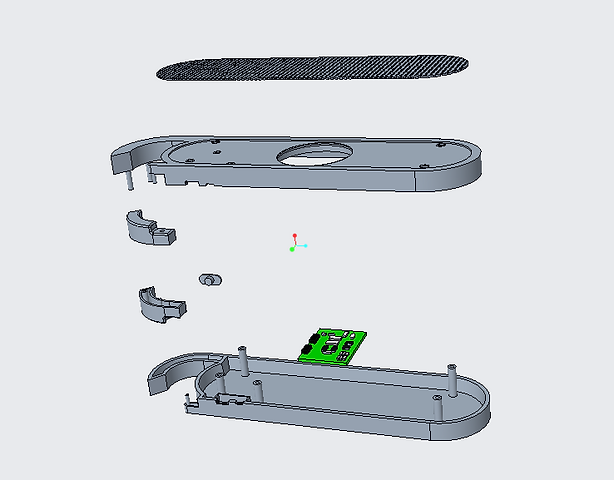
Manufacturing Cost Analysis
Another crucial step in evaluating this product is to perform a manufacturing cost analysis. Using the CAD model above, I was able to use aPiori to help estimate the approximate cost to manufacture a single product. However, during this analysis, I had to leave out the circuit board, loudspeaker, and battery as those are components that cannot be analyzed by the software and will be most likely purchased. I, then, compared this cost to the 'catalog price', which is the cost to create this product if the all the components were purchased from retail stores. As seen from the first table, it is easier to manufacture the product specific parts and purchase the general parts (screws, battery, etc). Using this information, we can calculate the optimal cost (seen in the second table) that was implemented to create the Bluetooth speaker.


Screenshot of aPriori program doing a cost analysis of one of the speaker components
Redesign Ideation
As seen in the previous sections of the design challenge, the product had many areas that needed to be improved. I wanted to be able to improve the recyclability of the product while also ensuring I am able to improve upon the manufacturing and assembly (DFMA) aspects of the product. Accordingly, I came up with 3 potential different designs that meet these criteria:
Concept 1: Snap Fit Assembly
With this concept, I aimed to reduce the manufacturing costs by removing the need for screws and instead, replacing them with snap fit mechanisms. Furthermore, improved upon the product's recyclability by also eliminating the need for the many internal pins and holes and thus, reducing the amount of plastic used in the product. By creating a snap fit assembly, this also eases the process for assembly and disassembly, which makes for a better product in terms of manufacturing (as it reduces assembly time) and recyclability (as the components can easily be disassembled and reused without any damage). Below is a diagram representing the concept and some initial ideation notes:
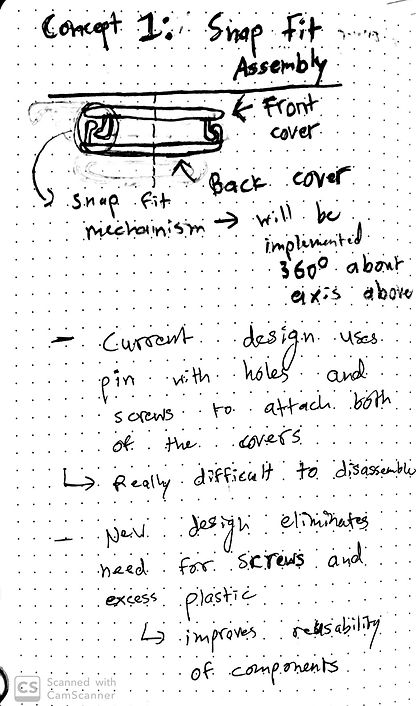
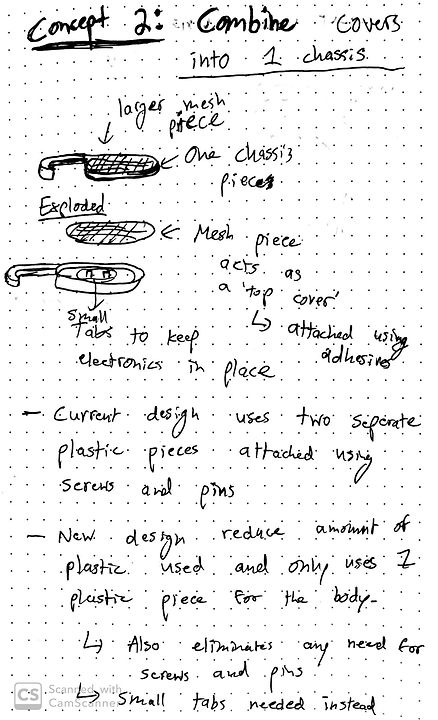
Concept 2: Combine covers into 1 body piece/chassis
​
For this concept, I decided to combine the top and bottom covers pieces into one chassis piece in attempt to reduce manufacturing costs, ease assembly times, and greatly improve upon the recyclability of the product. In this design, I plan to extended the bottom cover piece to encompass the entire internal components and then, increase the area of the speaker mesh grill such that it acts like a cover on the top of the speaker. This mesh grill will be assembled with the main cover using adhesive bonding. This way one can completely eliminate the need for any unnecessary components such as screws or snap fits and keep it relatively simple.
Concept 3: Change material of clip
​
Unlike the previous 2 design concepts, this one focuses on improving upon the recyclability and functionality of the product. In order to completely avoid the chance of the clip interfering with main body of the speaker, I thought about replacing the cylindrical steel bar that will rotate about the pin as usual, but due to its shape and structure, it will be able rotate more freely around the pin. Since the clip will not be manufactured with plastic and instead, a more recyclable material will be used, this will also improves the product's recyclability potential. Unfortunately, this change will also increase the manufacturing cost.

Pugh Selection Matrix
To help compare and decide between the various design concepts, we can implement a Pugh Matrix and see how each concept affects the overall quality of the product. The quality of product depends on various qualitative and quantitative factors as listed in the table below. From the Pugh Matrix, I can safely conclude that Concept 2 is better redesign model to implement.

Redesigned CAD Model
Since we are redesigning the product based on Concept 2, we have essentially change the design of only 2 components: the bottom cover piece and the speaker mesh grill. The rest of the pieces will remain the same and be assembled almost similarly as before. The new redesigned CAD models for those two components and final exploded view can be seen below.
Redesigned Cover

Redesigned Speaker Mesh Grill

Final Redesigned Assembly

Design of Experiment: Testing the Strength
Regarding my redesigned product, a major concern of mine is the strength of the product itself from damages. Since the main selling point of the bluetooth speaker is that it is easily portable and the user can carry it with them anywhere, the product itself will have to sustain basic stresses and strains in compared to other speakers before the product is damaged. As a result, the design variables that will be involved would be the thickness of the material/component (measured in mm), type of material used, and the number of internal supports. In order to test the strength of the product, I plan to measure the pressure/stress applied (in Pascal) needed to break the product physically.
There are other various factors (e.g. temperature, type of assembly, etc) that can also affect the strength of the product, but for the purposes of this experimentation, we assume those factors to be constant.
Each of design variables will be only have two levels of design with a high (+1) and a low (-1) value. The thickness, material, and support values was determined based on a common range of qualitative/quantitative values seen in most Bluetooth speaker products.
Ideally, a manufacturer would want the target values for their strength of their product to be as high as possible. However, in the real world, there are physical limitations to the amount of pressure a certain product can withstand. Hence, the target value for the stress that the product should be able to handle should be between 40 - 55 MPa.

Since this is a 2 full factorial design experiment with 3 varying factors/parameters, then 2^3 = 8 different tests will be conducted. Each test will undergo 3 exact same trials in order to ensure consistent, accurate data is being taken. The following is the experimental matrix for this DOE:

Now, in order to see which of the following design variables actually has an affect on the strength of the product, I generated hypothetical experimental data as seen in the table below. We use this data and use statistical methods to see which factors affects the strength. First, I calculate the average, standard deviation, and variance of the responses for each test. After that, I calculated for the main effects and compared that to the system 2 sigma value to see which variables had the biggest affects.




In the end, it can be observed that the 4 main factors can affect the strength of the product: x2, x12, x13, and x23. As seen from the last table, it can be concluded that the type of material (x2) and the combination between material and internal supports (x2x3) must be maximized in order to create a strong product. Additionally, the combination between thickness and number of supports (x1x3) and the combination between thickness and type of material (x1x2) must be minimized. Therefore, the only possible combination that satisfies these conditions is low level design (2 mm) for the thickness, high level design (ABS Plastic) for the material, and high level design (5) for the internal supports.
Final DFMA Analysis and Conclusion
After spending all that time during ideatation and redesigning the Bluetooth speaker, I can conduct another DFMA analysis on this new product and check to see whether my product has improved in terms of manufacturing costs and assembly times.
For a cost analysis, we will use aPriori again for the new components and then, create a new table that shows the total cost to manufacture this product:

As I did before, we can also perform a DFA analysis to calculate the DFA index and check whether the new product has a better assembly process or not (main changes have been highlighted in yellow):

In conclusion, the redesigned product has proven to be better than the original better in terms of manufacturing costs and assembly process. I can also safely conclude that the redesign preserves and maintains the original functionality and overall quality of the product. Not only does this indicate that the new redesign is cheaper to manufacture and assemble, but also shows that the product is more sustainable/eco-friendly in general. Why? Since I eliminated components to lower manufacturing costs, this also reduces the amount of plastic that ends up in the environment and thus, leaves a better 'footprint' than before. Besides that, since I also made the product easier to disassemble, this will make the product easier to disassemble at a recycling center (which saves time and money) and many of the speaker's components can be re-used. All in all, this ends up being a win-win situation for all of the stakeholders involved and the environment.